- Pharmacy buyers scramble to find additional stock or alternatives for the shortage medication, often paying a premium to buy any stock remaining in the marketplace
- Pharmacy managers must reconfigure the various pharmacy automation systems that carry the affected inventory to make sure those systems continue to function as expected with temporary formulary changes
- Pharmacy leaders communicate any changes to the availability of shortage medications to providers and nursing staff to ensure patient safety
- 340b sites have to start accruing for new NDCs, potentially resulting in the write-off of previous accruals for the shortage medication
Occasionally, however, a shortage can be so severe that the FDA issues guidance allowing pharmacies to extend the expiration date for the affected medications. This happened in August due to a shortage of several Pfizer-manufactured NDCs of Sodium Bicarbonate, Atropine Sulfate, Dextrose, and Epinephrine. The theory is that by extending the expiration dates of these products, more inventory is kept in the supply chain reducing the impact of the shortage. In reality, however, many of these drugs still get thrown away at or prior to the original manufacturer’s dating.
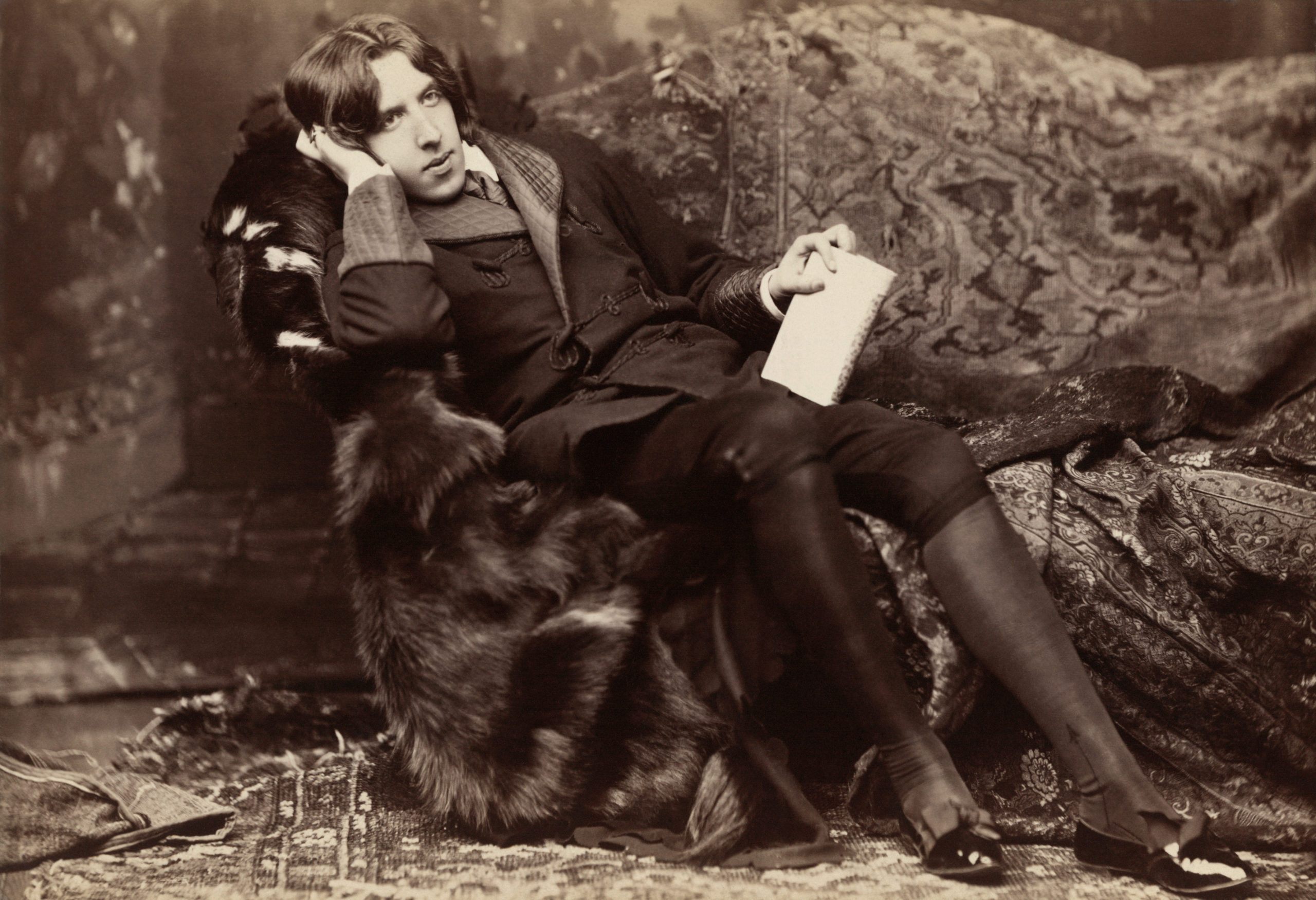
“It is always with the best intentions that the worst work is done.” – Oscar Wilde
Many pharmacies fail to leverage extensions
A hospital pharmacy’s ability to take advantage of expiration extensions is dependent on automation system flexibility, staff resources, and awareness. The flaw in dating extensions comes down to three issues:
- The team members processing the medications need to remember that there is an extension in place for the affected medications. Shortage inventory may stay in the supply chain for months and people often forget the related changes, if they are even aware of the extension in the first place.
- A hospital staff member has to touch every package, find the NDC and lot number for the package, and compare it to the list of NDC and lots that are included in the extension. Given the wide variety of inventory systems, distribution systems and physical storage locations for medications, manually checking every unit of the affected medication in the hospital would require hours upon hours of staff time.
- Many of today’s pharmacy automation systems don’t track down to the NDC and lot level for every package. When the system does track this information, it is usually tied to a pocket or bin, not to specific units.
As an example to elaborate on this third point, Anesthesia workstations don’t reliably track the NDC and lot of every unit currently in the cabinet. These gaps occur either because the cabinet doesn’t include those data points as input fields or because pharmacy staff doesn’t take the time to update the item-specific information on every restock. This lack of specificity in the data often means that precious outdated inventory is thrown away (and, with it, the opportunity to lessen the impact of the shortage) or many unnecessary man hours are spent hunting for affected units.
Pharmacies need item-level visibility
Kit Check is different. We track the NDC, lot and expiration date for every package in your kits and trays, as well as in your tagged shelved inventory. The restocking process assists staff by identifying exactly what needs to be fixed, including any outdating issues, before the kit, tray, or Anesthesia workstation liner can be sent back out. Kit Check reporting provides on-demand visibility into the counts and specific location of any specified NDC and/or lot number. As a result, our customers are able to:
- Quickly understand the impact of the shortage on both kitted and shelved inventory
- Easily extend expiration dates where appropriate for all affected items in one easy action
- Consistently avoid throwing away usable inventory
Our customers can also quickly see opportunities for reduced or adjusted par levels within and across kits based on actual consumption data using our Segment Optimization Analytics. Our kit management tools also provide pharmacy managers the option to temporarily institute reduced par levels using our Alternate Fill feature to maximize their inventory and further mitigate the impact of the shortage.
Effective communication is still a barrier
We recently analyzed customer drug usage patterns while working on new machine learning algorithms. We were surprised to find that many of our customers had not yet extended the dates on the shortage inventory included in the August FDA guidance. There were almost 25,000 packages that were included on the FDA list that still carried the original manufacturer expiration date.
In reaching out to customers to understand why they hadn’t extended the expiration dates, the most common explanation was that they just didn’t know about the extension. That isn’t surprising. A similar issue with recall communication and awareness led to the creation of our Network Recall feature. Network Recalls has had a significant impact on ensuring our customers are aware of and can take timely action on recalls impacting their inventory. Although we don’t have a “Network Shortage” feature in the application yet, our cloud architecture allowed us to identify customers with significant quantities of still-not-extended inventory. We reached out to them to make sure they didn’t miss the opportunity to mitigate the impact of this shortage on their operations.
Interested in learning more about how Kit Check can help your team? Contact us.