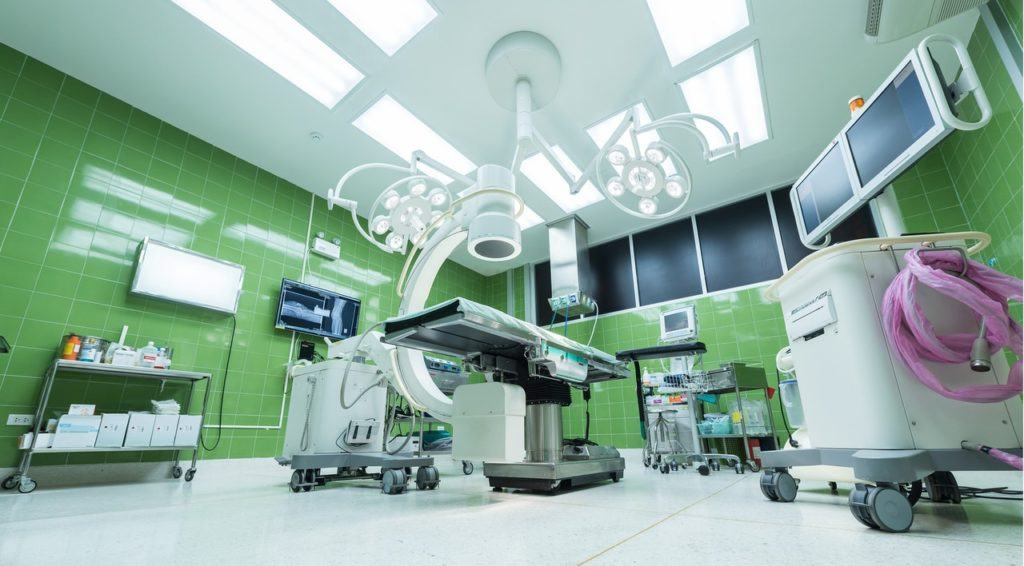
Regulatory compliance risks and missed optimization opportunities
I would have thought that, very infrequently, we would find a hospital that utilized anesthesia technicians to restock automated anesthesia workstations or manual anesthesia carts in the individual operating and procedure rooms. As it turns out, this practice is more widespread than I would have imagined.
Besides the obvious regulatory concerns of not having pharmacy involved in the dispensing and control of anesthesia medications, opportunities for optimizing and improving medication processes are generally lost. My experience is that Anesthesia technicians have a variety of jobs and tasks to perform and when given medication ordering, dispensing and handling, it is just not their top priority.
Pharmacy staffing and anesthesia concerns are barriers to change
When I talk with Pharmacy leaders about why they continue to leverage Anesthesia Techs to restock meds in the OR, two main concerns surface.
- Pharmacy lacks staff capacity to take over this function
- Anesthesia concerns about losing “control” and stockouts
In many instances, these two concerns lead Pharmacy to stay with the status quo. Based on my experience, however, both of these concerns can be overcome with a little bit of automation, regular analysis of utilization and a commitment from Pharmacy to really help improve practice for Anesthesia.
Automation, analytics and a focus on improving provider experience are key
For example, Edward Hospital recently presented a webinar on how they were able to improve medication visibility and workflow in the OR. To summarize their presentation, moving to a tray/liner swap model they were able to ensure Pharmacy oversight over medication restocking to ensure compliance. In addition, they were able to make this switch without increasing Pharmacy staff because of the efficiencies offered by Kit Check.
As it relates to Anesthesia concerns, Edward Hospital was able to leverage Kit Check Analytics to really understand Anesthesia workflows and help provide a better experience. Through looking at waste and usage patterns, they were able to:
- Build a business case for switching to prefilled syringes (Pharmedium) for some high-waste medications.
- Optimize tray layout to ensure most frequently used drugs were easily accessible to providers.
- Decrease par levels for slow movers to free up space and increase par levels for fast movers to eliminate stock-outs.
This is just one example of how Kit Check has been instrumental in assisting Pharmacy departments take control of the medication distribution process in the perioperative space over the last several years. As a result, our clients have been able to eliminate stock-outs, improve regulatory compliance and improve Anesthesia and Pharmacy staff satisfaction.