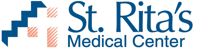
Pharmacist Tray Processing Time Cut by Nearly 80%
When restocking pharmacy kits manually, pharmacists at St. Rita’s spent an average of two hours of each day. Using Kit Check, the pharmacy was able to cut labor time by 79.6%, down to only 24.5 minutes per day for all 230 trays that they manage in the system. Kit Check users independently report time savings ranging from 71% – 96% so St. Rita’s results are right in the middle.
Kit Check Data is an Efficiency Gold Mine
To up the ante beyond time saving within the pharmacy walls, St. Rita’s put a process in place to monitor staff performance for tracking the location of the trays within the hospital at large. Previously, there was zero visibility into whether the right kits were in the right place. St. Rita’s staff could only determine tray locations by going out and looking at each and every one. Kit Check has allowed the team to track trays down to a specific room in the hospital.
By leveraging the Kit Check activity reports, St. Rita’s can identify which technicians were in need of additional training to make sure everyone was up to speed. This has allowed them to continue striving towards their goal of 90% kit location accuracy. Kit Check is well known for delivering pharmacy kit and code cart medication stocking accuracy increases of 99.5-100% and St. Rita’s is extending the benefits to kit distribution and location accuracy.
More Data Benefits – Reducing Waste Due to Expiration
Location tracking is just one piece of St. Rita’s workflow that the team has automated with Kit Check data. Using the Expiring Soon report, which is sent to the team on demand monthly, St. Rita’s can identify kit medications in the hospital that will be expiring within the next 30 days. They can then easily retrieve and reallocate them to other departments in the hospital where they can be used before expiration to decrease cost of medication waste. Furthermore, pharmacy managers use the NDC Assigned to Segment report to monitor the accuracy of their Kit Check formulary.
State Board of Pharmacy Approval
An additional benefit St. Rita’s gained from implementing Kit Check is that they have been able to eliminate the pharmacist double-check on their trays. St. Rita’s states that their inspector from, “The Ohio State Board of Pharmacy approved that RFID technology can eliminate the pharmacist double-check process,“ provided that they conduct a manual audit on a small percentage of their kits. This has led to tremendous labor savings, as pharmacist time can “instead be devoted to patient care activities.”
Driving First-Year ROI of 75%
Combining reduction in expired medications, labor savings, and medication error cost avoidance, St. Rita’s estimates a first year return on investment (ROI) of 75% and a seven-year ROI exceeding 90%. St. Rita’s story is common among Kit Check users. Hospitals consistently report measurable savings in multiple areas along with their appreciation of the more consistent and efficient process. Whether you’re considering Kit Check for your OR anesthesia workstations, crash carts, or anything in between, our team is as friendly, eager, and responsive as we were when we started back in 2012.